6 Steps to Building an OSHA-Compliant Hazard Communications Program
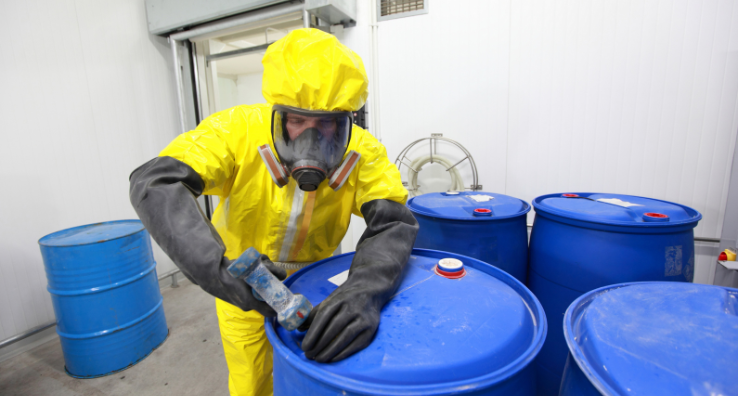
It’s common to associate hazardous chemicals with images of barrels of toxic liquids and large pools of waste. But in reality, even common substances like paints, cleaners, degreasers, or detergents in your workplace may be considered hazardous chemicals. Without an effective hazard communication program, you could be putting workers at risk and face financial penalties.
Missing or inadequate hazard communication programs was OSHA’s #1 cited issue last year in the general industry sector. There was a total of 2,424 cited violations, which moved it up from the number two spot the previous year when it was second only to respiratory protection.
Chemical manufacturers and importers are required to classify the hazards of chemicals they produce or import. All employers are required to provide information to their employees about the hazardous chemicals to which they are exposed. OSHA requires this to be done through a written hazard communication (HazCom) program, labels and other forms of warning, safety data sheets, and training. Distributors are required to transmit the required information to employers.
An effective HazCom program ensures all hazardous chemicals in your facility are identified and labeled, and that you have up-to-date, properly written safety data sheets available. It also includes provisions for training all potentially exposed employees on chemical hazards, safe handling, and protective measures.
The hazard communication standard applies to any chemical which is known to be present in the workplace in such a manner that employees may be exposed under normal conditions of use or in a foreseeable emergency, with a few exceptions. If your employees have potential exposure to hazardous chemicals and you need a HazCom program, here are six steps to help you get started.
- Inventory Chemicals
The first step to creating a HazCom program is to inventory and classify any hazardous chemical your facility produces, imports, handles, or creates through the mixing of different substances. Before you begin, we recommend reading 29 CFR 1910.1200(b)(5 & 6) so you’ll know what the exceptions are for certain chemicals.
This can be a significant undertaking for larger facilities. But don’t leave any stone unturned in your search. Your program’s effectiveness will depend on the accuracy of your hazardous chemical inventory. Your facility must have this list present and accessible to employees and auditors. - Determine Who Could be Exposed
After creating a list of chemicals in the facility, you’ll need to develop an equally thorough list of the positions and people who handle hazardous materials and could be exposed during normal operations or in an emergency. This critical step of the process ties directly into your training. - Label Materials
OSHA has specific marking and labeling requirements for different types of containers. It’s important for employers to know these requirements in detail and ensure that containers are marked appropriately in accordance with 1910.1200. Labeling requirements can include: product identifier, signal word, hazard statements, pictograms, and precautionary statements. the name, address, and telephone number of the chemical manufacturer, important, or other responsible party should also be included.
Employers can use signs, placards, process sheets, batch tickets, operating procedures, or other written materials instead of labeling individual stationary process containers. OSHA requires this information to be in English. You can add the information in other languages to the material, as long as the information is presented in English as well. - Obtain and Maintain Safety Data Sheets
If you are a chemical producer or importer, you’ll be responsible for classifying hazards of chemicals you produce or import. Other employers having potential exposure need to maintain a safety data sheet for each hazardous chemical they use, with some exceptions referenced in step 1.
If your chemical supplier did not provide a safety data sheet, it’s up to you as the employer to obtain or create one. Developing them on your own is an intensive process to cover 16 sections from chemical composition and accidental release measures to fire-fighting measures and toxicological information. See the full list here. - Train Employees on Chemical Hazards
Once you’ve covered all the bases of identifying the hazards and determining who could be exposed, you can begin training employees to make them aware of the information they need. Training should include multiple topics such as location and use of safety data sheets, locations and operations where chemicals are present, the contents and functioning of the HazCom program, lists of chemicals, protective measures, and other information specified in the HazCom standard.
The Intertek Alchemy workplace safety training library includes training sources on chemical safety, safety data sheets, GHS pictograms, and more. The full catalog is available here.
Employees must receive this information on their initial assignment, and whenever a new chemical hazard the employees have not previously been trained on is introduced into their work area. For example, training should be updated and delivered when you introduce any new product or process that alters the hazardous chemical landscape of your operations. That’s also the time to update your safety data sheets. Also, employers must decide how often they want to conduct refresher training.
- Maintain Records for Audits
In addition to an overarching concern for the health and safety of your employees, safety data sheets and training records should be continuously updated and readily available for OSHA inspectors.
OSHA typically doesn’t conduct routine audits except for some specific industries. They will inspect targeted facilities, for example in the event of fatalities, severe injuries, or worker complaints.
Penalties from these inspections differ based on the nature and severity of violations. The penalty for a single first-time serious violation can exceed $15,000. If the violation is repeated or OSHA determines it is willful, the penalty can surpass $156,000.
Please contact us if you need help developing your HazCom program. Intertek also provides Safety Data Sheet authoring services for chemical producers, importers, and exporters. We have consultants on hand who can evaluate your situation and provide advice and resources to help ensure the safety of your employees and prepare for questions or audits from OSHA.