Surprise! It’s OSHA! Now What?
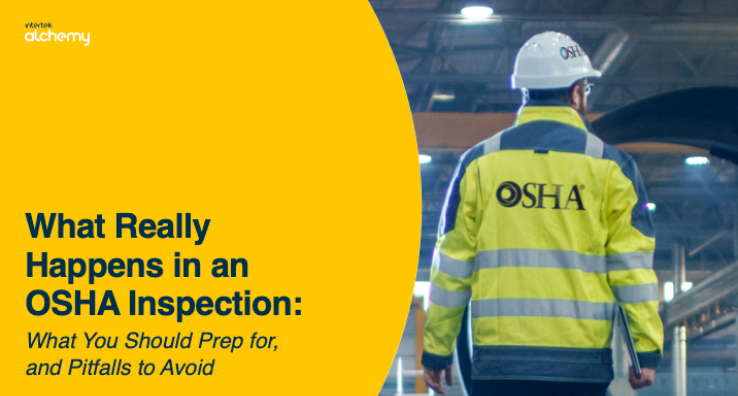
“OSHA is here.” As a manufacturing safety or operations officer, you probably don’t want to hear these three words at work.
Last year, the Occupational Safety and Health Administration conducted over 31,000 inspections, nearly half based on employee complaints, injuries, fatalities, and referrals. Citations and penalties from these inspections ranged from $15,625 to $156,259 per incident.
Many businesses find these inspections intimidating and overwhelming. But that doesn’t always have to be the case.
In this blog, I’ll walk through what to expect during an OSHA inspection, and how to prepare and avoid the most common mistakes.
Understanding the Basics
But first, let’s address the basic components of an OSHA inspection and what to expect when an agent comes to the door.
The first thing to know is that OSHA inspections are rarely announced ahead of time. However, they can be pre-announced for several reasons, such as if someone believes there is imminent danger at your worksite. Inspections might need to be scheduled after hours and with specific management or worker representation. An OSHA area director can also notify you of an upcoming inspection if they believe it’s necessary to ensure a more thorough inspection. Inspections almost always happen if a complaint has been filed or a serious injury is reported.
You can deny entry to inspectors and ask for a warrant. If you do, they’ll go get one and they’ll always have one if they must come back. This is a great way to get off to a bad start.
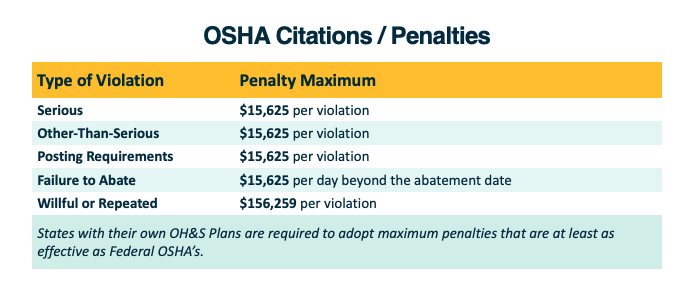
The Three Phases of an Inspection
OSHA breaks its inspection process up into three parts: the opening conference, the walkaround, and the closing conference.
During the opening conference, OSHA inspectors meet with employer and employee representatives to explain the purpose of the inspection, including hazards called out in a complaint. They’ll also examine safety logs and summaries of reported injuries and illnesses.
The employer and employee representatives will then accompany the inspector for a walkaround phase to check hazards identified in the complaint or incident. While the inspection may focus on a defined scope, whatever the inspector sees is fair game. During this time, your entire work area is subject to inspection. Your employees have the right to private, voluntary interviews with inspectors. Employees can refuse to be interviewed and can have another person of their choice attend the interview. If the inspector refuses to allow that other person to attend, the employee can decline the interview. At the end of this phase, any apparent violations will be brought to management’s attention onsite.
After a walkaround, inspectors will organize a conference to talk with employees and management about their observations. These meetings may be held separately with employees without management present. They’ll discuss what they discovered and corrective actions to address safety issues. Any potential violations and penalties will be presented during this time.
This covers what to expect. Now, here’s what you can do to be ready.
Five Pitfalls to Avoid During an OSHA Inspection
Once an inspection is underway, there are several ways to help make the process easier or harder. Here are five common mistakes companies make during an OSHA Inspection.
1. Lack of an expert to accompany inspectors
As part of the process, companies can and should have a qualified escort to join inspectors. The word “qualified” is key because that person should fully understand and be able to communicate your OHS program in detail, answer questions correctly, and know how to find and provide requested records.
Remember inspections are mostly unannounced, which means you should always have a qualified escort ready and available for every shift. The last thing you want is to miss an opportunity to provide good information during an inspection or have someone assigned who can’t answer questions or produce records. Failure to answer questions and provide records increases your chances of a citation.
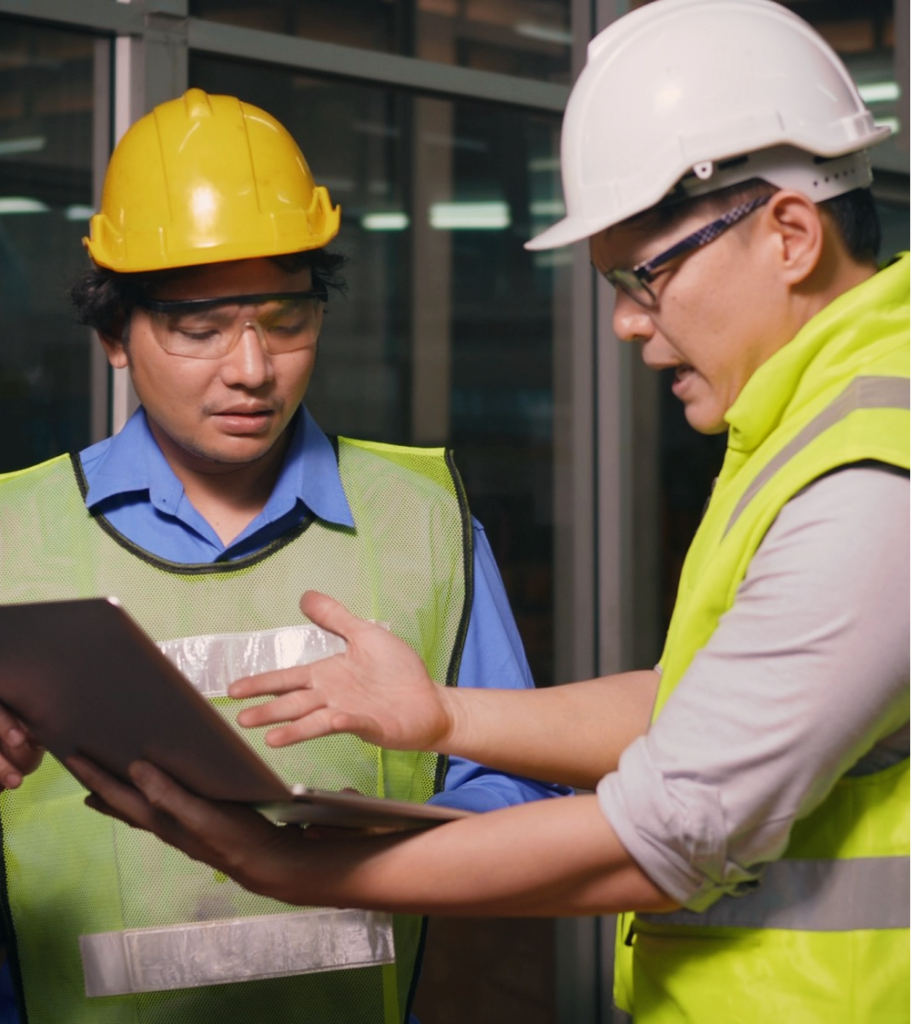
2. Debating with inspectors
Even if you love a good debate or feel you’re being treated unfairly, now is not the time to argue with the inspector. Remember, inspectors are people too, dedicated to ensuring a safe workplace for everybody. They share your concern for the well-being of your employees. So, never allow yourself to get defensive, evasive, or hostile. That will only make things worse. Cooperate whenever possible. That doesn’t mean you have to voluntarily show them everything. But be courteous and responsive to their questions.
3. Inadequate training on safety policies and procedures
From OSHA’s perspective, having a strong OHS policy is only the first step to ensuring a safe and healthy workplace. Policies are meaningless if employees don’t follow them. Remember, inspectors will canvass the floor and talk with employees about their work environment. They’ll quiz them on safety policies and may ask them to demonstrate their work.
They may even seek an area where they can observe an overall shift in action. That’s why it’s critical for employees to be constantly trained on your OHS program and procedures, and that you have the records to demonstrate their participation and comprehension. Make your life easy in the regard with an all-in-one safety training content, delivery, and reporting system.
Remember, health and safety training is never a one-and-done job. It requires training whenever an employee is introduced to new hazards, ongoing refresher courses, always-on reminders like posters in the break room, and tightly maintained record keeping to verify and demonstrate who has been trained.
4. Inadequate response to citations or weak corrective actions
When an employee is injured on the job, it’s not enough to simply say they didn’t follow company policy. OSHA encourages companies to conduct a root cause analysis (RCA) of incidents, including near misses. Proof of an RCA can help you effectively respond to citations.
A solid RCA will be the basis for an effective corrective action to prevent the incident from reoccurring. If you receive a citation from OSHA, follow up with a thorough and well-documented RCA and corrective action, including a plan for verification of effectiveness. This will show OSHA and your co-workers that you’re serious about preventing recurrence. An inadequate response can lead to further harm, repeat violations, and increased penalties.
5. Not being prepared for OSHA in the first place
Hopefully, this article will help you be better prepared for an OSHA inspection. But there’s so much more to learn and do. Three important elements of preparation include:
- Having a comprehensive, well-maintained OHS program in place.
- Providing adequate safety training during onboarding and maintaining adequate job-specific safety training.
- Having the ability to document and retrieve everything an inspector might want, including employee training records, safety logs, training courses, RCAs and more.
Multiple tools and resources are available to help you develop and maintain an OHS program. OSHA provides a set of guidelines, Recommended Practices for Safety and Health Programs. ISO 45001 is a specification standard for comprehensive OHS management systems and can take your organization beyond compliance. If you are not ISO Certified, resources are available to assist with ISO 45001 certification.
Of course, an independent review is often a good idea. Intertek Alchemy provides safety consulting services including OSHA compliance assessments, as well as assistance with corrective action response if an inspection has already occurred.
Contact us with questions. We’re here to help.