Emergency Action Plans: Preparation is Your Best Defense
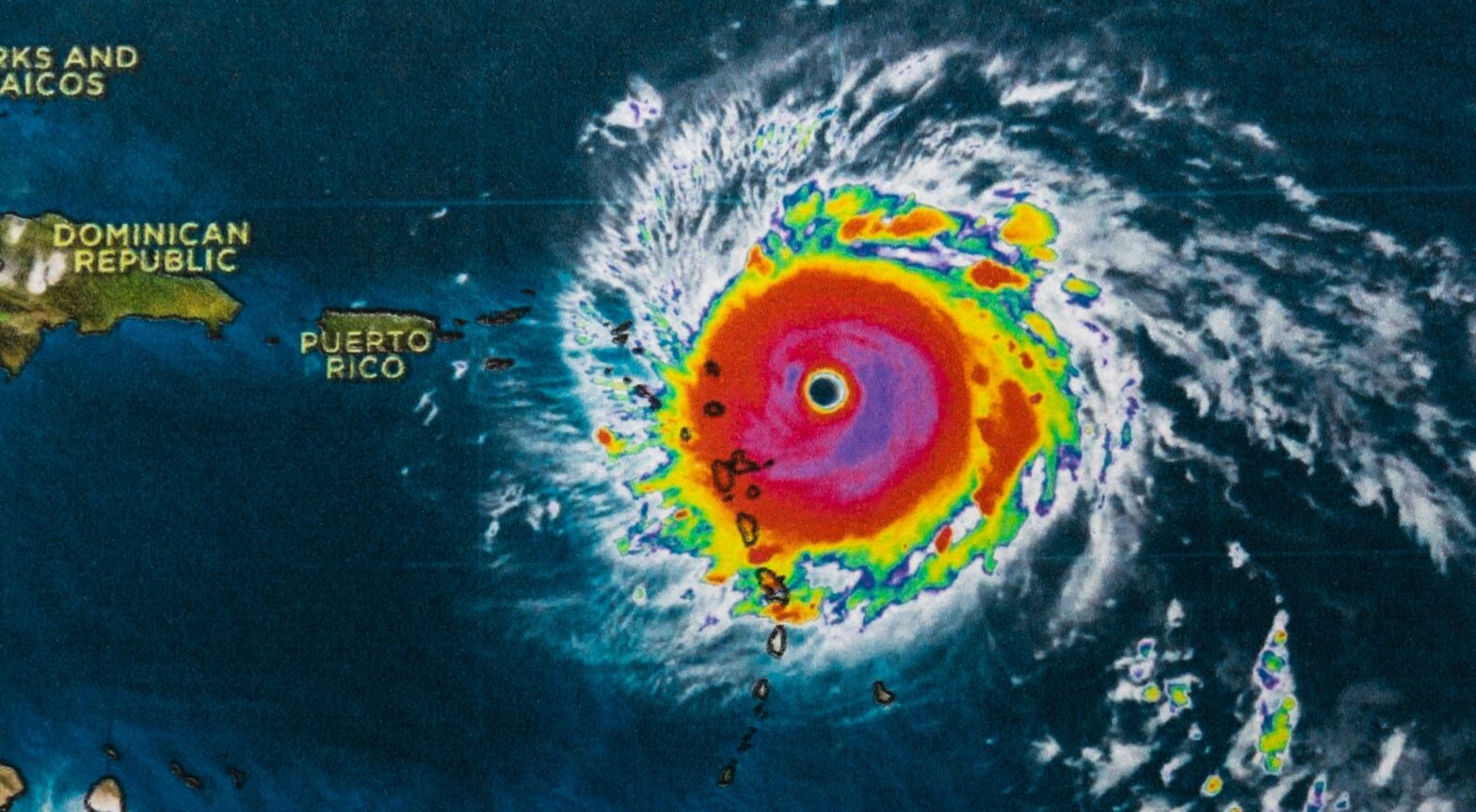
With significant environmental impacts in the last year made from hurricanes Harvey and Irma, and problematic weather ahead, it’s imperative to have an emergency action plan in place. In fact, OSHA requires all workplaces with more than 10 employees to develop a written Emergency Action Plan (EAP) that identifies and coordinates necessary employer and employee actions during an emergency.
Emergencies have been happening for centuries. Here’s a brief look at a few incidents from history, reasons why companies need emergency action plans, and how to train your frontline workforce to take smart action in the face of danger.
A History of Emergencies — Without Action Plans
In 1911, at the Triangle Shirtwaist Company in New York, a fire broke out in the three upper floors. Tragically 146 young girls died because there was no way for them to get out of the building.
In 1991, Hamlet, North Carolina, at the Imperial Food Products facility where they prepare cooked chicken, a hydraulic line ruptured and poured hydraulic fluid into some of the vats that were cooking the chicken. A dense, dark fluid, a petroleum based fluid, ignited and filled the facility with a dark, heavy cloud of smoke. And as employees tried to evacuate they found out:
- There was no lighting provided.
- The exit doors were too far away.
- The owner of the facility had chained some of the doors closed to prevent stealing.
As a result, 26 employees died and the company received $808,000 worth of citations.
How could both of these incidents have been avoided?
Create an Emergency Action Plan
An Emergency Action Plan protects employees from fires, chemical releases, tornadoes, earthquakes, and hurricanes. It should also include responses to workplace violence incidents. No one can predict when an emergency or disaster may occur within the workplace, therefore having an emergency response plan in place is critical in case of:
Toxic Material Releases
For example, many use ammonia as a refrigerant. Yet, ammonia can be very toxic. It travels in a cloudy vaporous form, and if it travels through the plant and possibly leaves the plant, it could create an ongoing hazard as it moves through the facility.
Physical Hazards
Fire chemical hazards and releases of particular chemicals. What might occur in that situation? Again, if you’re under PSM, you’re going to be looked at by OSHA if they come into examine your PHA’s, your Process Hazard Analysis, and under HAZWOPER, in terms of how you have addressed the issue of who’s going to respond if anyone to the emergency to try to evaluate it, control it, shut it down, become the incident commander.
Civil Disturbances and Workplace Violence
We work with many clients whose Emergency Action Plans unfortunately now include active shooters. What do we do if there’s an active shooter, and do we have provisions in there? What do you tell employees about running, hiding, and resisting? What do you have in our Emergency Action Plan that relates to workplace violence?
Any Other Internal or Unique Sources
It’s important to talk to your employees. And those of you who are subject to process safety management know that there’s a specific provision that requires employee participation. We should be talking to our employees. This should not be all from the top down — it should be coming from the bottom up. Find out any potential emergencies that could disrupt your workplace and then start going through the process of what if. Anticipate the unanticipated to the extent that it’s possible, and prepare for that.
Consider the Impact: Plan for Worst-case Scenarios
What if all your power crashes, so your emergency alarm system crashes and you don’t have a backup? Or your lighting system goes out and you don’t have a system to get people out? What are you going to do? Who is going to lead people out? Many times you think you have a solid backup system, and it doesn’t kick in. What are you going to do in that situation?
Your EAP should include:
- A designated person to lead and coordinate emergency plans and evacuation
- Maps created from floor diagrams with arrows that easily designate evacuation routes, exits, and assembly points
- Selected employees to assist those with disabilities or who do not speak English
Train All Workers On EAPs, Regardless of Age, Language, or Full-time Status
If you are the host employer and you bring other employers and their employees to your work site on an ongoing basis, or temporary basis, you’re responsible for their safety and health.
Harm in case of emergency or disaster at that particular facility may result in OSHA citations or criminal prosecution against the host employer. All employees, regardless of work status, must know the Emergency Action in place. A multi-touch safety training solution that engages frontline workers is the best way to get everyone aligned in case of emergency.
Want to learn more about putting an effective emergency action plan in place? Watch the free webinar.