How to Define a SMART Leading Indicator: A 5-Step Plan
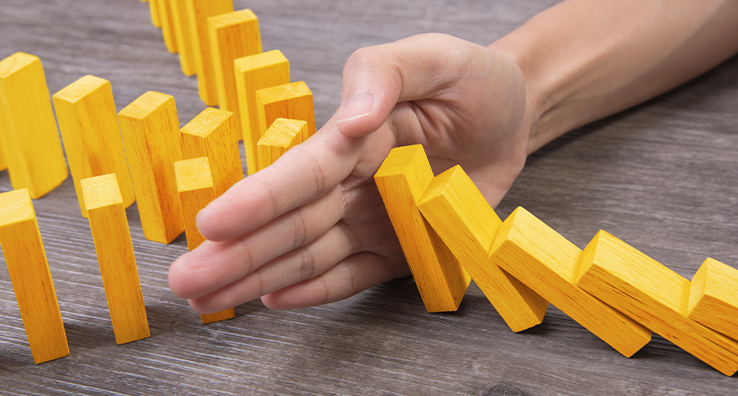
Leading indicators are one way to provide line of sight into future performance, as well as indicate how you have performed so far. By balancing the use of leading indicators with lagging indicators, you will get an overall comprehensive understanding of exactly where you are and what you need to do, to get to where you want to be.
Joy Inouye, a research associate at Campbell Institute at the National Safety, recently shared key insights and information gleaned from her long history in this field.
So how to get started?
1. Look at What’s Already Being Measured
Could any data that you’re already collecting be used as a leading indicator? “Organizations collect a lot of data on a regular basis,” says Inouye, “so it is highly likely that there is already a ton of information available from your company that could be leveraged as a leading indicator.”
If that’s the case, great! Now you don’t have to go out of your way to collect. You can use the data you have to identify at-risk areas in your operations and what actions to take for mitigating those risks in the future.
2. Just Get Going — Don’t Spend A Lot of Time Deliberating
Inouye shared an anecdote where the experts she worked with spent two whole years trying to decide which leading indicators to track. They were under the erroneous impression that they had to roll out a full suite of 10 leading indicators instead of picking just one thing to focus on. All that time wasted when they could have been tracking and collecting data instead!
Start simply and start small with one or two leading indicators and go from there. “Just get started!” she says.
3. Make Sure Indicators Communicate Meaningful and Actionable Information
“Your leading indicators and the data produced should give you an indication of what to do and where to go,” says Inouye. If you see certain numbers rising or falling, that should give you an indication that it’s time to stop and evaluate. Is what you’re doing working? How is it impacting other leading or lagging indicators?
Ask: “Where do we need to be and what do we need to do?” and make sure your indicators support your goals. Otherwise, this becomes a simple data collection exercise — and no one wants to collect numbers for the sake of collecting numbers
4. Obtain Leadership Support
For anything you really want your organization to do well on, you’ll need to make sure you have the support of your leaders. This doesn’t mean that executives need to be in the nitty gritty of choosing leading indicators, but they should understand the overall goal and what leading indicators you’ve selected so that they can help drive success. Pro tip: have leading indicators that track at a corporate level to obtain support across the organization!
5. Integrate Leading Indicators Into Overall Safety Management
Now is where you do something with all of that data you’ve collected! Your indicators should have meaning behind them and shouldn’t hang out separately from your EHS management system. “They should feed back into your program to make a meaningful impact,” says Inouye. This essentially means that your leading indicators need to be balanced with a correlation against your lagging indicators to measure their success. If you don’t see a reduction in risk or injury rate, collecting data on leading indicators is merely an exercise without any action or meaning.
For more in-depth exploration on leveraging employee training as a leading indicator for your EHS program, watch our webinar “How to Utilize Employee Training as an
EHS Leading Indicator: Tips from the Pros” or download the slides.