Hygiene: Get Your Employees on Board
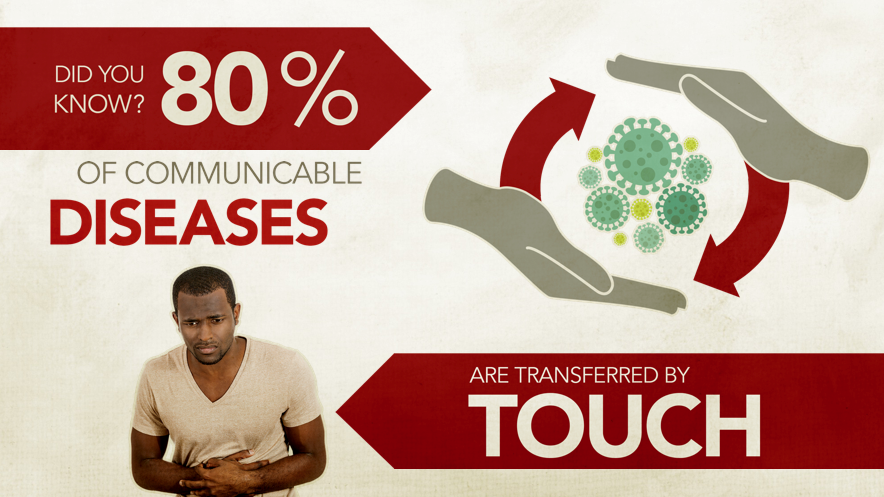
Although publicity around food safety incidents sometimes seems to show the food industry in a bad light, the ongoing prominence of food safety in the national news should be viewed positively by food processors if for no other reason than this: our employees—including our frontline food workers—pay attention to the news, too. So, when food safety training events come around, it should be that much easier for training managers and supervisors to capture workers’ full attention. And when training addresses the specific topic of personal hygiene, we have a great opportunity to bring the message home—literally.
Good personal hygiene begins at home
Good personal hygiene means maintaining cleanliness of the body and clothing before arriving at the plant. And it almost goes without saying that employees displaying symptoms of communicable illness should not be at work and certainly should not be allowed to handle or work around food. Clean and sanitized uniforms, smocks, coats, and aprons should be kept and put on at the workplace to minimize the risk of outside contamination. On the plant floor, hair falling into food can contaminate products both microbiologically and physically, so hairnets and beard covers are an absolute necessity. Sleeves should completely cover hair on arms.
Staying clean in the workplace is a challenge. Soiled outerwear should be changed as soon as possible. Footwear procedures requiring the use of shoe covers, captive footwear, foot baths, and floor foamers should be strictly followed to ensure shoe-borne contaminants are not tracked into clean production areas. Handwashing procedures—with close attention being paid to thorough cleansing of easily missed areas like nail beds, the tops of hands, forearms, and wrists—are critical.
All these concepts and precautions are generally well known. Food companies train employees on them specifically. Still, contaminations and non-conformances happen, many resulting from lapses in hygiene. So how can food processors make sure that employees become engaged, stay engaged, and put into practice the enormously important practices of personal hygiene after training is complete?
Get the word out—and help them get the picture
Communication is the key. Message reinforcement tools such as visually impactful posters, dynamic digital signage, topic-specific team huddle guides, and mobile on-the-floor coaching apps can all keep the urgency of personal hygiene at the forefront of employees’ minds. They’ll also help processors avoid the consequences of hygiene topics being forgotten or ignored. These tools share messaging and imagery across all media and are available in a full range of customizability, from out-of-the-box basic all the way up to completely proprietary with exclusive internal branding.
Posters can be positioned at key hygienic control points, such as dressing areas, handwashing stations, and entries and exits to clean zones. Digital signage located in main hallways, lunch rooms, and break areas are an engaging way to remind workers of the crucial relationship between personal hygiene and food safety. Scripted, vividly illustrated huddle guides encourage dialog around hygiene topics directly at points of use on the plant floor. And mobile coaching apps facilitate one-on-one observation and documentation of proper hygienic procedures. They also represent another means of encouraging dialog between supervisors and frontline employees.
Wash, rinse, repeat
The best intentions in the world, supported by the best training, will go a long way toward ensuring that frontline food workers take the subject of personal hygiene seriously. But inevitably, someone will miss the message or simply forget. Visually and emotionally engaging reinforcement tools are food processors’ not-so-secret weapons in the battle for food safety. If they seem like overkill or perhaps an unnecessary extra expense, consider the cost of a recall due to food borne illness. Message reinforcement tools, in that light, are pretty inexpensive insurance. One recall avoided will more than cover the cost of any premium.