IAFP 2015 Takeaway: Sustained Food Safety Culture
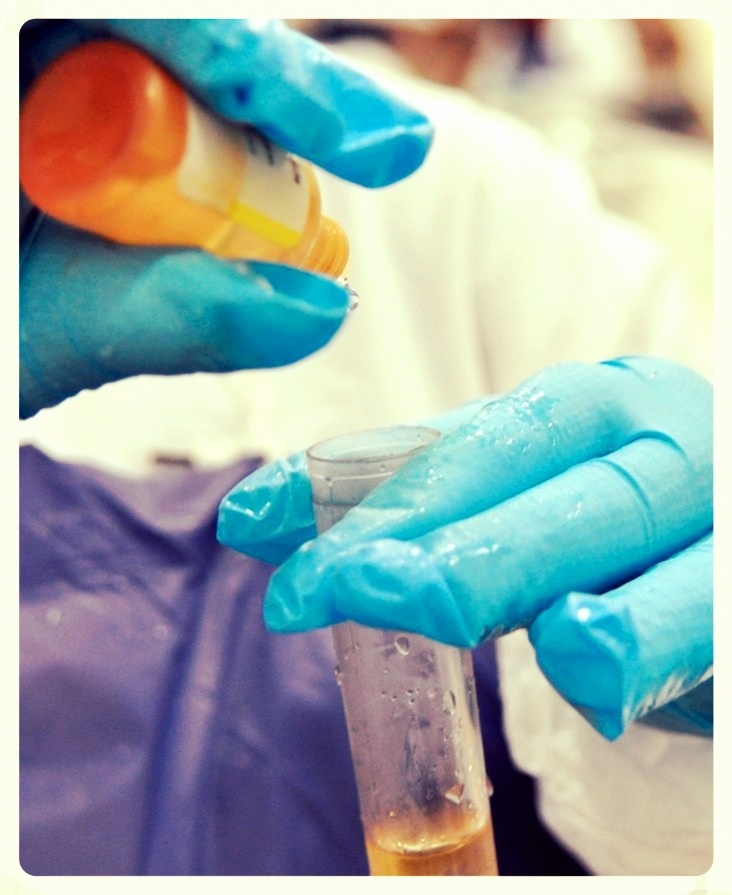
I believe many IAFP attendees would be in agreement that the core of any food safety system starts with preventative controls and environmental monitoring. That’s why Alchemy pulled together a panel of some of the industry’s finest to lend their expertise on Environmental Monitoring: a preventative control requiring the closed loop method of food safety education at this year’s IAFP Conference in Portland, Oregon.
Pamela Wilger of Cargill, and Laura Dunn Nelson of Alchemy moderated the session which featured Dr. John Butts of Land O’ Frost, Holly Mockus of Alchemy, and Miriam Eisenberg of Ecolab. In case you couldn’t be there, here’s a breakdown of the session’s key takeaways.
Designing an Effective Environmental Monitoring Program
Dr. John Butts addresses the audience at IAFP 2015 in Portland, OR
Dr. John Butts of Land O Frost outlined the basics of an effective environmental monitoring program. First and foremost, he iterated processors should approach these programs knowing that an effective program will yield positive samples.
A positive sampling result must be treated as a success! It means your program is working.
Here are the 5 key steps:
- Identify where the “good” positives can be found.“Good” positives are swab results that give you actionable results that enable you to improve your preventative controls. Know where to go looking for them.
- Create a measurement system.When creating a measurement system understand the “behavior” effects. This way you can incorporate it into the closed loop approach and better understand what behaviors to reinforce.
- Incorporate verification monitoring.The verification monitoring program consist of zones which should be routinely sampled for pathogens. Use randomization of sites selected or randomize times that sites are sampled. If positives are found schedule and complete the appropriate corrective action. Be sure to document – if you didn’t document it many times means you didn’t do it!
- Define the process of environmental monitoring. Note interventions and preventative measures that are designed and put into place. Look for root causes that are clearly identified and be sure that the workforce is trained to fully understand preventative practices and processes.
- Cover all potential indicator sites.Indicator sites give a broad overview of the effectiveness of your critical control points. Be sure to include large areas that collect spatter, note that composite sampling is acceptable.
Creating behavior change
Holly Mockus of Alchemy Systems discussed how to engage employees to fuel a culture of food safety. She talked through the next element of the closed loop in behavioral reinforcement.
Holly gave a case study example from her tenure in the food industry. She noted, shutting down plant production in this instance yielded any number of findings. Things like slow flowing drains, hollow doors allowing water to collect and drip, seeping curbs became easy to spot in a dry environment.
The biggest takeaway from this root cause analysis uncovered a complete lack of employee engagement and resulted in a corrective action that mapped out the following elements of behavior change.
Elements to behavior change
Communication
Communication is a means of connection between people to exchange knowledge, information, news, feelings and emotions.
Training and education
Training and education is the act or process of imparting knowledge to improve job performance and impart cultural norms.
Inclusion
Inclusion is recognizing that you work as “one” even though your functions are not the “same.”
Awareness
Awareness is being well informed in order to exhibit accepted cultural practices even when no one is looking.
Observation
An observation consists of watching a behavior or practice in order to gain an understanding of what is being done for the purposes of correction and reinforcement.
Reinforcement
Reinforcement is not please and thank you. It is recognizing a behavior, praising or correcting that behavior AND recognizing the outcome of the behavior.
Model corrective observation process
Using this approach, employee behaviors and compliance can increase up to 26 percentage points. Holly cited Alchemy’s recent behavior change study and noted this data helped to develop the Alchemy Coach mobile application which won IAFP’s Food Safety Innovation Award this year.
Closing the Loop with Employee Communication
Miriam Eisenberg of Ecosure, a division of Ecolab, closed out the session by covering the last element of the closed loop method – employee communication. She stressed the importance of well developed, consistent, and constant two-way interactions.
Her advice to senior management teams was to be sure communication happens both top-down and bottom-up to ensure food safety systems remain secure. She then shared some case studies in successful food safety cultures, including resources from the FDA.
The top takeaway Miriam communicated was that employees should always understand “how” and “why” they are required to follow processes and procedures.
Elements for effective communication include:
- Listening – Use regular, verbal communication between supervisors, trainers, and employees
- Reading – Keep up to date, printed materials including signage, huddle guides, shift notes
- Watching – Incoroporate videos, live demonstrations, posturized story boards
- Doing- Use hands on training and communication techniques
- Repeating/Validating/Coaching – Make sure to repeat and reinforce desired behavior
- Bridging language, education, generation gaps – Understand where communication may break down and develop strategies to overcome those obstacles
Eisenberg also stressed the importance of role modeling. Employees learn from and communicate with people they trust. It is important to never talk over your employees’ heads, respect where they are coming from and recognize how to relate to them.
Final Thoughts
Basic human psychology comes into play when creating a sustained culture of food safety and environmental controls are no exception. By applying these experts’ advice companies can begin to fortify their programs and empower workers with the knowledge they need to step into tomorrow’s leadership roles.