Improving Operations with Statistical Process Control
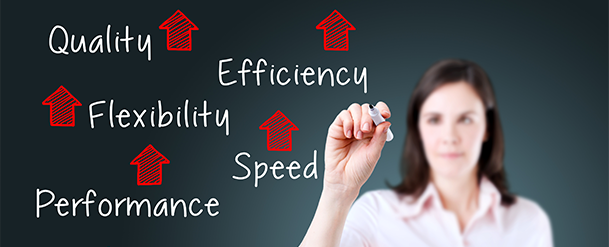
Statistical Process Control (SPC) is top of mind for the food industry. The recent changes to the SQF Quality Code have prompted new interest, since additional requirements for SPC training and applications have been added to the code. In addition, progressive companies recognize the benefit of using SPC applications throughout the manufacturing process at key process control steps.
New SQF Quality Code Requirements
So, what’s new with SQF? Quite a bit! The SQF Code changes for Edition 8 effective 1/2/18 eliminated the prior SQF Level 3 certification and replaced it with an independent SQF Quality Code that companies have to be certified to maintain equivalency with prior Level 3 certifications. This change benefits SQF suppliers by not penalizing SQF Food Safety audit scores due to quality related non-conformances. It also helps suppliers establish effective quality process control systems to reduce customer complaints and out of specification product.
The Management Responsibility Section 2.1.2.5 iii specifically requires the SQF Quality Practitioner “be competent in statistical process control (SPC) and/or other quality tools to reduce process variation and drive root cause analysis of non-conformities.” As a result, many QA professionals need to take initial or refresher training on SPC to obtain and demonstrate this competency to auditors. Alchemy’s Professional Services and many other companies offer this service to help meet the training needs of the industry.
The Product Sampling, Inspection and Analysis Section 2.5.4.3 specifies that “statistical process control methods shall be used to effectively control and optimize production processes to improve process efficiency and product quality and reduced waste. Control charts shall be in use for control of key processes and have defined upper and lower (process) control limits (+/- 3σ).”
To comply with this requirement, suppliers must consider where the right Critical Quality Points (CQP’s) should be identified in their operations. These CQP’s should correlate with key Product Specification Requirements as applicable for attributes such as Water Activity, pH, product dimensions, weights, or others.
The old days of just having a CQP for net weight or lot code checks are gone. SQF has raised the bar for the expectations of Food Quality Plans. These plans should drive process control and product consistency to reduce complaints and improve customer satisfaction. For CQP monitoring, SPC control charts such as a X Bar and R chart must be used to document results of process consistency during daily monitoring. These charts must identity the target value with upper and lower control limits within 3 standard deviations. This controls the process with results graphed to visually represent the process control and prompt corrective actions when necessary if results are out of target ranges. Suppliers should reassess their Food Quality Plans well before their recertification audits in order to meet the new requirements.
SPC for Process Control for All Manufacturing Companies
SPC still makes great sense — even for companies not certified under the SQF Quality Code. SPC is a great quality tool all companies should use for key quality points. SPC can be used for cost control savings that helps companies improve profitability. SPC also plays a key role in helping companies achieve operational excellence. For example, we have seen companies use SPC successfully to reduce costs from excess giveaway weights over stated net weights in finished packaged products and reduce waste from out of specification products during processing. These controls increase product yields and decrease the cost of quality failures to maximize profitability.
Final Thoughts
QA Professionals should take time to learn and use quality tools, including SPC and other, to continuously improve their quality systems. Operations managers should embrace SPC to improve process consistency and control costs. SPC can be your friend to drive substantial improvements throughout an organization. There are also great software and systems, such as Safety Chain and Infinity QS, that can do SPC easily for you, eliminating confusion from the process. Bottom line? You won’t regret investing the time to do SPC right — the return on investment alone makes it worthwhile.