OSHA’s 7 Elements to Creating a Safe and Healthy Workplace
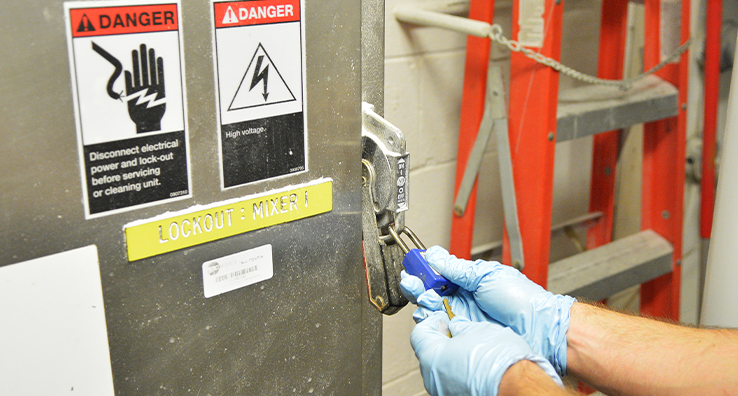
When working to meet OSHA’s health and safety requirements, you might find yourself motivated by both the carrot and the stick. Being responsible for employee safety can be a rewarding experience, providing you the opportunity to learn, and to improve your co-workers’ health, safety, and quality of life. At the same time, this position carries great responsibility and the risk of personal liability.
Maintain compliance, and you can reduce employee accidents, decrease worker compensation claims, avoid penalties, and improve overall productivity. Fall short of the agency’s requirements, and you run the risk of creating an unsafe work environment. Not only will this result in low morale and high turnover, it also exposes your company to hefty fines and the potential for civil lawsuits that could cost millions.
OSHA can be overwhelming. Anyone who has held a paper copy of OSHA’s general industry standards knows there are nearly 800 pages of dense content covering rules for health and safety aspects for every facet of operations.
However, during my years of working as a consultant, auditor, and trainer, and helping companies meet health and safety requirements and pass audits, I’ve found OSHA to be highly supportive. The agency is forthcoming with tools, resources, and guidance. When I’ve called or emailed a state or federal OSHA office for help, I’ve always gotten a timely response from a qualified OSHA professional who provided the answers I needed.
OSHA also provides a blueprint to help you build your workplace health and safety program. This recommended framework will help you map out your company’s formal approach to keeping employees safe and healthy at work.
An effective OH&S program requires the support of every employee, from the frontline workers to the executive level. OSHA recommends building your workplace safety blueprint on these seven elements.
Management Leadership
No workplace safety program can be successful without the support of the company’s top management to provide leadership, vision, and resources. You also have to ensure employees are aware of the company’s executive support. Senior management has to lead by example in providing a safe and healthy workplace.
Worker Participation
A workplace safety program requires the participation of your entire workforce, including contractors and temporary workers. You have to gain their input while setting goals, identifying and reporting hazards, investigating incidents, and tracking progress.
Employees must be encouraged to make suggestions and to report safety and health concerns without fear of retaliation. Any potential barriers or obstacles to worker participation in the program such as language, lack of information, or disincentives should be removed or addressed.
Hazard Identification & Assessment
Establish procedures that continually identify workplace hazards and evaluate risks. Examine all processes and tasks, ranging from the routine to the extraordinary, to identify related safety and health hazards. Remember to include support processes like utilities, maintenance, and facilities in addition to production processes. Periodic inspections and reassessments should follow your initial assessment to identify new and changing hazards.
All incidents, including near misses, should be investigated to determine their root causes, as this will help you identify hazard points. We recommend that you document your process for hazard identification and assessment in a formal procedure, and maintain documentation of the process outputs. This part of your program is also an opportunity to develop a comprehensive catalogue of the OSHA standards that apply to your operations. That catalogue will provide critical information you’ll want for the next section.
Hazard Prevention & Control
As a team, identify and select methods for eliminating, preventing, or controlling workplace hazards. The catalogue of applicable OHSA standards that you developed during the previous stage will provide you with a starting point because they will include the minimum legally required controls.
Always apply the hierarchy of controls to the best of your ability, in the following order: Elimination, Substitution, Engineering, Administrative, and Personal Protective Equipment. Then, develop a plan to implement the controls starting with the highest priorities. Provide interim protection where needed, track progress, and verify control effectiveness.
Workforce Training and Education
Everyone should be trained to understand how your program works and carry out their assigned responsibilities. Managers and supervisors should receive training that explains their responsibility to protect workers’ rights and respond to reports and concerns. And all workers should be trained to recognize workplace hazards and understand how to report them.
Training is one of the most critical aspects of your health and safety program. Properly trained and engaged employees are the number one defense against injuries and illness. It empowers your entire workforce to recognize and help correct hazards before they result in illness or injuries.
Your health and safety program should identify the type and frequency of your training events and how they’re delivered and tracked. OSHA requires companies to provide training in the appropriate language and context. Using standard training technologies, such as a digital audience-response platform connected to a learning management system (LMS), ensures your employees understand their training and automatically documents their comprehension.
If you have gaps in your health and safety training courses or training platform, you can save time and money by using third party providers. The Intertek Alchemy safety training platform, for example, includes dozens of tried and true courses used by over a thousand manufacturing facilities.
Program Evaluation & Improvement
Periodically evaluate control measures to ensure they are effective. Establish processes to monitor program performance, verify program implementation, and identify program shortcomings and opportunities for improvement. Take necessary actions to improve the program and overall safety and health performance.
Communicate and Coordinate with Host Employers, Contractors, and Staffing Agencies
As you gain support within the four walls of your company, you should also demand a commitment to health and safety from your host employers, contractors, and staffing agencies. This means they must communicate the same worksite hazards and protection procedures. Before beginning work, host employers, contractors, and staffing agencies should coordinate work planning and scheduling to identify and resolve any conflicts affecting safety or health.
This is just a high-level look at what it takes to develop a health and safety program, based on OSHA recommendations, that will help you meet your legal requirements. If you’d like a deeper dive, check out our eBook Be OSHA-ready Every Day: A Guide to Compliance Readiness that takes a deeper dive into OSHA and the steps needed to build a successful Safety Plan.
And if you’d like some more personal, individualized attention, please contact us to discuss an OSHA Compliance Assessment and implementation.