Q and A: OSHA Top 5 Violations in General Industry
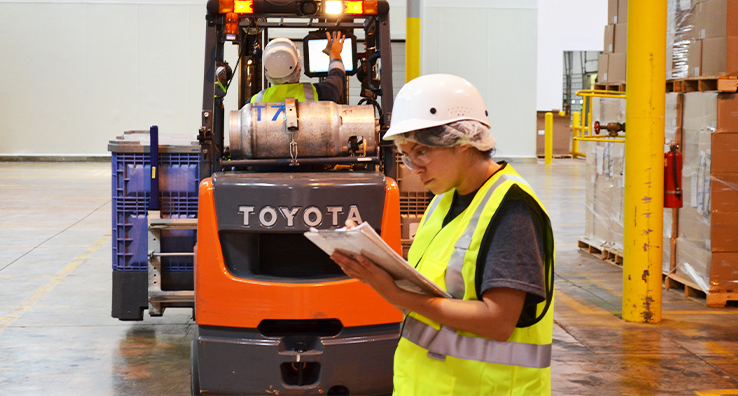
Rick Gehrke, Senior Environmental Safety and Health Consultant here at Intertek Alchemy, recently hosted the webinar “Don’t Get Busted! OSHA 2019 Top Five Violations in General Industry” that covered the specific standards, the hazards and types of associated incidents, penalties, as well as some of things that you can do to protect your people and your organization.
We caught up with him after to ask some of the most commonly asked questions in regard to these OSHA violations.
1. What are the top 5 OSHA violations?
The most frequently cited standards in General Industry, based on 2019 data from OSHA are as follows:
- Hazard Communication (1910.1200)
- Control of Hazardous Energy – Lockout/Tagout (1910.147)
- Respiratory Protection (1910.134)
- Powered Industrial Trucks (1910.178)
- Machine Guarding– General Requirement (1910.212)
2. In general, why or how do you think these violations typically happen?
There are several reasons behind these violations, including:
- the employer’s lack of awareness of the requirements
- a shortage of resources including qualified staff
- lack of organized programs
- employer disregard for the law
- employees’ refusal to follow the organization’s procedures.
Based on my own direct observations over the years in many industries, violations of OSHA regulations result mostly from a lack of knowledge and a lack of resources.
Most of the successful organizations I’ve worked with are serious about health and safety. They recognize the value of their people and want to protect them. If they’re not doing something they should be, it’s because they didn’t know. When I point out the gaps, they fix them. Unfortunately, sometimes this isn’t the case. Some of the violations cited by OSHA inspectors are willful or repeat violations. These are situations where the employer knew there was a requirement but didn’t follow it, often because of the short-term cost outweighing the long-term benefits of compliance.
3. Have you noticed any commonalities or trends?
If we look back over the history of OSHA violations in general industry from 2014 to 2019, we can see that the top listed violations have stayed pretty much the same. The cited standards are those that apply to the most commonly present and commonly dangerous hazards, with large numbers of people exposed.
Another trend to watch is enforcement activity and resulting public reporting of violations. OSHA has limited resources and is subject to the fickle winds of politics. According to the OSHA website, “Federal OSHA is a small agency; with our state partners we have approximately 2,100 inspectors responsible for the health and safety of 130 million workers, employed at more than 8 million worksites around the nation — which translates to about one compliance officer for every 59,000 workers.”
That’s a lot of ground for a few people to cover. The point is that we as responsible employers cannot rely on OSHA enforcement to protect our people. The responsibility is ours.
4. What are some common misconceptions that most people hold about OSHA violations?
Here are a few examples of erroneous ideas that people have:
- OSHA hasn’t visited or fined us, so we must be okay.
- We haven’t had any serious injuries, so we must be doing things right.
- The employees aren’t complaining, so they must feel safe.
- We’re a small company and we don’t use lots of hazardous chemicals, so our legal requirements are minimal.
If you’ve caught yourself thinking any of the sentences above, it’s time for a reality check!
5. What are the ways to prevent Injuries and Illnesses and avoid citations and penalties?
There are four key steps to take to ensure safety and prevent bad practices:
- Know the regulations that apply to your organization.
- Obtain and maintain the resources, including qualified people, time, and materials, to build, maintain, and improve the programs needed to comply with the regulations.
- Implement a formal OHS management system, for example based on the requirements of ISO 45001.
- Commit to going beyond compliance and continually improving your organization’s occupational health and safety performance.
Thanks for your insights and expertise, Rick!