Workforce Training: Are You Doing These 5 Things?
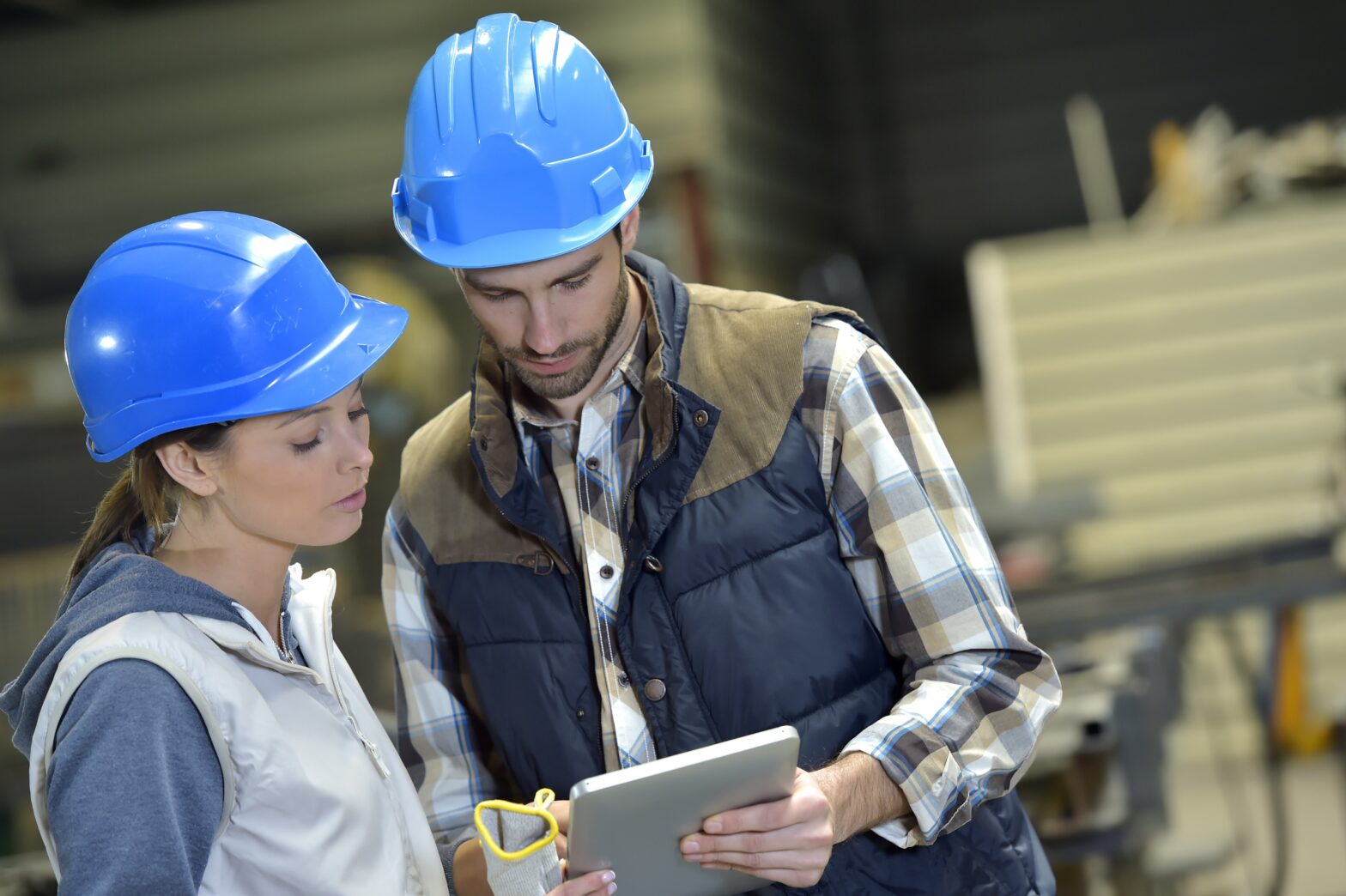
In the past, employee training mostly took place during onboarding. New hires got showered with information they were expected to retain well enough to apply correctly on the floor. Not surprisingly, this “spray and pray” method has proven less effective with time, as today’s learners experience the world visually and digitally, with one topic rapidly moving to the next.
These days, learning programs that focus on reinforcement for continuous improvement are becoming the industry standard because of higher success rates. It makes sense. Safety is never “one and done,” and it’s often when employees get too comfortable that accidents happen. Unfortunately, in our industry, accidents mean much more than a simple slip and fall. Accidents can lead to incidents, injuries, and even death.
The most effective training programs rely on a systematic process of validation and reinforcement to ensure important concepts are understood. First comes understanding, and then comes correct action on the floor. While more training that focuses on engagement might seem a strain on already lean workforces and resources, there are several effective methods that may be easily incorporated into most safety programs, even immediately.
Here are a few ways to elevate your training program:
1. Develop learning plans to streamline training
Automating training is one way to standardize processes and procedures, especially when scaling for larger operations. Developing learning plans, essentially play-lists of required courses that supervisors may “plug and play,” makes training more efficient. Learning plans can be tailored according to role or department, saving time rather than reinvent the wheel for each new hire. Learning plans have also been known to empower employees by allowing them to “own” their training and development.
2. Use central reporting for easier audits
Another method of streamlining training is to use a central reporting system. One area of training that is always difficult to manage is compliance documentation. Between evolving regulations, high turnover, and often analog documentation methods, tracking training can be a chore. An automated system, like internal auditing, that enables audit-readiness makes sure training and corrective actions are documented and stored in the cloud for easy retrieval.
3. Use shift huddle guides for more efficient meetings
Shift huddles led by supervisors are an effective way to reiterate important training concepts and get everyone on the same page. It’s also a valuable opportunity for face time and allows supervisors to address the group and answer questions at once. However, shift huddles may vary depending on the supervisor. Not every supervisor is skilled at leading meetings or managing time. Many leading companies have found success using pre-determined shift huddle “guides.” Not only do they save time by providing supervisors with a blueprint, they help meetings stay on track and keep messaging consistent. For more mileage, multilingual guides can be used to reach everyone on diverse teams
4. Reinforce — and repeat —for best results
Studies show that up to 80% of training material can be lost within the first 30 days — unless that material is reinforced. Workers are more likely to retain information that’s delivered continuously, and in a quick, efficient manner. The best way to deliver information quickly is in short learning “bursts” or mini-lessons that reinforce major concepts introduced in training. Shorter lessons are not only easier to digest and remember, they can be conducted quickly, often on the line. Because in manufacturing every minute matters, using “down time” to deliver mini-trainings can maximize your training program’s efficiency.
5. Elevate training with one-on-one “coaching”
The most effective training involves some level of one-on-one coaching, ideally performed on the floor. Many regulations require formal observations; however, finding the time can be a challenge. Some companies have seen success using a mobile app that observes, verifies, and tracks corrective actions in the cloud. Record as you coach for 24-hour audit –readiness, make staying compliant that much easier.
While there are as many ways to strengthen safety training, and many depend on resources, budget, and culture, these five methods may be implemented at most facilities right away for an immediate improvement in employee enagement.
How have you taken training to the next level at your workplace? Share with us in the comments below!