5 Grinder Safety Tips to Prevent Workplace Injuries and Deaths
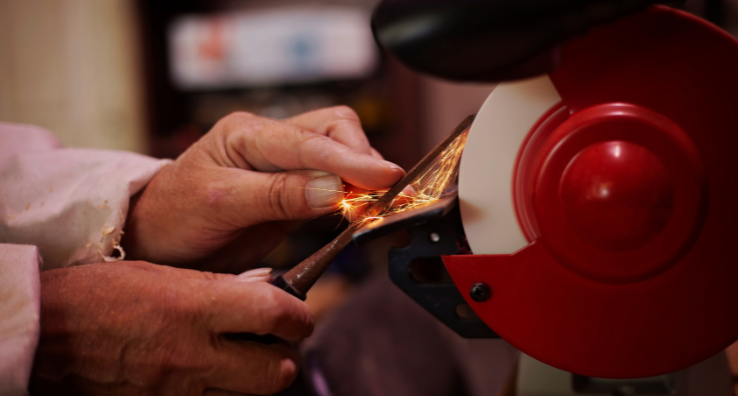
Abrasive wheel grinders are standard tools for most manufacturers, especially if you have a mechanical or maintenance shop onsite. When not checked and maintained, or used incorrectly, they can cause severe injuries or deaths. There are lots of different types of grinders including bench grinders, pedestal grinders, angle grinders, and more.
This article is mainly about the first two. Bench grinders and pedestal grinders both do basically the same job.
According to an OSHA review of 27 grinder accidents in an eight-year span, more than 26% resulted in employee deaths. The most common accidents occur when employees get their clothing, fingers, or other parts of their bodies caught in a grinding wheel or when they’re struck by debris when the grinding wheel explodes or disintegrates. Finger and thumb amputations are extremely common.
These accidents are easily avoided through equipment maintenance and training. Unfortunately, people become complacent about grinder hazards or just don’t know how to inspect and keep them safe. As a workplace safety consultant, I often find grinders that are out of spec and could easily cause an injury or fatality. People using these machines need training, and we need to make sure that they get it.
The grinders we’re talking about here are usually mounted to a workplace bench or pedestal with two grinding wheels used to sharpen hand tools or grind other materials like metal. The grinding wheels are made of ceramic material and spin at high speeds, typically up to 3,600 RPMs. People can get hurt, badly, when those wheels become cracked, or protective guards are loose, missing, or not adjusted properly.
OSHA provides a checklist for abrasive wheel equipment grinders that, if followed, can reduce and prevent deaths and serious injuries. Here’s a quick overview of some safety standards that can be incorporated in ongoing inspections.
OSHA Grinder Wheel Safety Standards
- Do side guards cover the spindle, nut, and flange 75% of the wheel diameter? This is necessary to prevent injuries when a wheel comes apart. The pieces will stay contained within the guard and not fly around and hit the user or others nearby.
- Is the work rest used and adjusted to within 1/8-inch of the wheel? This helps prevent something like a shirt sleeve from getting pulled into the wheel and ensures that something doesn’t flip up and hit the user in the face.
- Is the adjustable tongue guard on the top side of the grinder used and kept to within 1/4 inch of the wheel? The guard must be within a quarter inch of the wheel to help contain pieces if the wheel comes apart. It also helps contain sparks.
- Is the maximum RPM rating of each abrasive wheel compatible with the RPM rating of the grinder motor? With any grinder, it’s critical to check the maximum RPM of the motor and ensure abrasive wheels are designed for it. The RPM should be marked on both the grinder and the wheel.
- Before new abrasive wheels are mounted, are they visually inspected and ring tested? Look for cracks, chips, or other signs of damage. Ring testing typically involves holding the wheel up in the air by a finger through the center and tapping it with a nonmetallic implement like a piece of wood or a plastic screwdriver handle. The wheel should make a ping sound. If it goes “thunk,” that means it’s cracked or otherwise damaged. Mark it as unusable and return it to the supplier or throw it out!
Other OSHA grinder safety checks include:
- Is cleanliness maintained around grinders?
- Are dust collectors and powered exhausts provided on grinders used in operations that produce large amounts of dust?
- Are goggles or face shields always worn when grinding?
- Are bench and pedestal grinders permanently mounted?
- Does each electrically operated grinder have a permanent, continuous, and effective path to the ground?
- Are fixed or permanently mounted grinders connected to their electrical supply system with metallic conduit or another permanent method?
- Does each grinder have an individual on-and-off control switch?
In many manufacturing sites, grinders are out of sight and out of mind until needed. Use the same consistent safety measures you require for commonly used equipment. Keep your employees safe from severe injuries and deaths by frequently checking your grinders and training your people to maintain and use them properly. Your workplace safety training program should include staple courses on machine guarding, PPE, and site-specific details that reflect your equipment
Contact us for more tips on grinder safety or a discussion on other equipment in your manufacturing site.