Batten Down the Hatches for the Manufacturing Headwinds of 2023
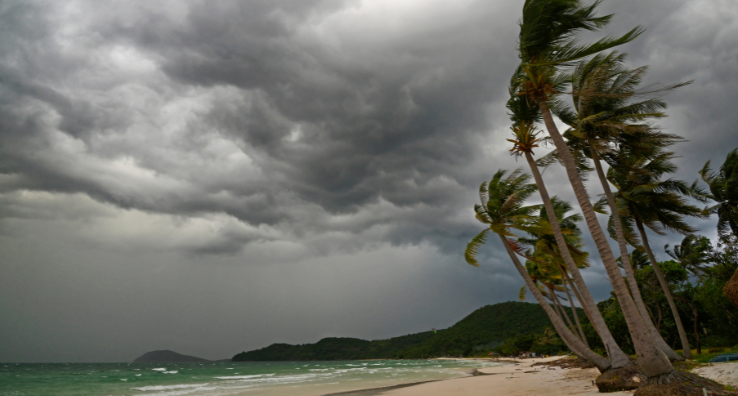
The new year can sometimes offer the promise of a clean slate and the chance to make improvements that take advantage of new opportunities. As much as I’d like to believe that’s the case for 2023, it’s not looking that way.
Unfortunately, too many challenges from the last two years will undoubtedly bedevil food manufacturers for several more months. Persistent labor shortages, stubbornly high inflation, and global instability will all likely be joined by evolving customer preferences, new regulations, and an unpredictable economy.
These factors will tremendously impact food safety, quality, and quantity, requiring you and other manufacturers to adopt new processes and training approaches. Let’s start by looking at the one issue that hammered manufacturers in 2022 – labor instability.
No Shortage of Labor Woes
The Great Resignation, also known as the Big Quit or the Great Reshuffle, roiled manufacturers as they scrambled to hire and retain workers after the pandemic. Millions of workers left in droves, complaining about issues like burnout, stagnant wages, and limited growth opportunities. Sadly, labor instability is expected to continue into this year. According to a recent PwC study, one in five workers say they are “extremely likely” or “very likely” to switch employers in 2023.
We know now it takes more than pay and bonuses to retain employees. It takes a combination of factors like a feeling of importance and opportunity for advancement, work/life balance, employee well-being, and healthy relationships with management. But one of the biggest reasons people leave their jobs is because of their supervisors, whether it’s a bad relationship or a lack of recognition.
Upgrade Learning & Development and Cross Train
That’s why it’s crucial to invest in leadership development. Being a leader isn’t just about knowing how to operate the machines. It’s about having leadership qualities and habits that foster employee loyalty and connections. Leaders must learn how to properly coach frontline workers, conduct constructive conversations, and resolve conflicts. The money spent on effective leadership training will far exceed the value of what you may spend on signing bonuses, which is why leading producers make the investment in leadership training designed specifically for manufacturing settings.
A path to advancement is essential to maintain labor stability and employee retention. Cross-training is a great example. It provides an employee the opportunity for growth, adds variety, and fosters new personal connections that encourages your employees stay on the job and prepares them for promotion. It also helps them understand the importance of their role within your overall operation. Of course, it can be a challenge to make time to provide structured cross-training and upskilling with so much focus on quotas and yield, which is why leveraging mobile training technology designed for the task is essential.
Radical Regulatory Changes Ahead
One of the food manufacturing industry’s biggest challenges this year is preparing for the FDA’s new food traceability requirements. These long overdue requirements will radically change how you manage data and track ingredients and products.
When the rules go into effect in January 2026, they will apply to many companies involved in the food production cycle, including the growing, receiving, transforming, creating, and shipping of foods. Companies will have to implement new processes for employees to maintain compliant paper documents and electronic copies.
Get Started Now
It’s a good idea to get a head start by determining if you manufacture, process, pack or hold any foods on the Food Traceability List. Familiarize yourself with the new terminology within the rules like Key Data Elements (KDEs), Critical Tracking Events (CTEs), First Receiver, Transformation, and Creation. And start improving communications with your suppliers and customers by engaging them on their recordkeeping plans
More importantly, you should get started now. This is not a valve you can turn on in December 2025. You’ll need to start putting the new processes in place and practicing and working out the kinks from your suppliers to make sure the data exchange is comprehensive, complete, accurate, timely and consistent.
Supply Chains Will Remain Messy
Even as global supply chains regain some stability, they remain highly susceptible to risks like labor shortages, cyber-attacks, transportation strikes, major weather events, global unrest, and a general lack of raw materials. Many experts are already predicting corn, bread, vegetable oil, and aluminum shortages.
As a food manufacturer, you must be prepared when your suppliers can’t deliver. You have to be able to quickly identify new suppliers or change processes and formulas on short notice. Lack of planning is where potential failure points can arise, creating potential risks to consumers and costly food recalls.
Plan for Alternative Sources
You can reduce supply chain risks by working with multiple vendors, auditing their food safety programs, and maintaining consistent communications. You should also review detailed product specifications, clarify expectations, and improve your change management skills.
There are three ways to help protect food quality and maintain production when your regular supplier fails to come through.
- Examine potential suppliers and their specifications for nutritional value, microbiological limits, regulatory compliance and food safety management programs
- Train employees to spot and report anything that doesn’t look or smell right with an ingredient shipment.
- Check supplier labels to compare them to product specifications to meet compliance specifications.
A Looming Recession is Bearing Down
Will we enter a recession in 2023? Many experts predict we will. But even as we hover outside what defines a recession, we continue to struggle through record inflation, keeping pressure on prices and higher wages as we compete in tighter labor markets. Soaring interest rates make investing in new equipment and infrastructure more expensive. As a result, I expect we’re in for some extreme belt-tightening in the months ahead.
During this time, you might want to cut budgets to delay repairs and upgrades, consolidate production, freeze new hires, reduce training, or downsize product packaging. These adjustments and changes must be well communicated to staff in order to prevent costly quality and safety errors.
While cost-cutting may be necessary, I always advise against cutting training. Research continually shows the more training and engagement frontline workers receive correlates to positive impacts on product quality, workplace safety, employee retention, and productivity. A comprehensive study specific to our industry with valuable insights on these topics is the Global Food Safety Training Survey.
You’re not the only one looking for ways to save a dollar. Consumers are rapidly shifting their buying preferences as they trade name-brand and organic foods for generic and inexpensive products. That means you might also be forced to reconsider the products you sell and the resources you put behind them.
Create an Agile and Lean Infrastructure
In addition to helping to retain employees, cross-training can help create an agile workforce that can be redirected when needed. If additional customer demand is placed on a different product or if you have to downsize products and relabel new packaging, your frontline workers will be ready to accurately manage the changes.
Lean manufacturing can help you save money, improve quality, reduce lead times, and improve service instead of implementing shortcuts that could lead to mistakes. To address these economic challenges consider creating new efficiencies and eliminating waste with lean manufacturing.
To assist your efforts, we recently rolled out the Alchemy Lean Manufacturing Training Library, which consists of 10 eLearning courses that help managers and supervisors identify and eliminate inefficiencies and production waste in their organizations.
Don’t despair. The year ahead is full of challenges and opportunities. Any adjustments you make this year can eventually become a means for long-term quality, processing improvements and a competitive edge in the market. Let us know how we can help prepare you for the headwinds of 2023. Contact us for more information or to speak with one of our consultants for an onsite assessment.