Five Ways You and Santa Can Ensure a Safe Workshop Year-Round
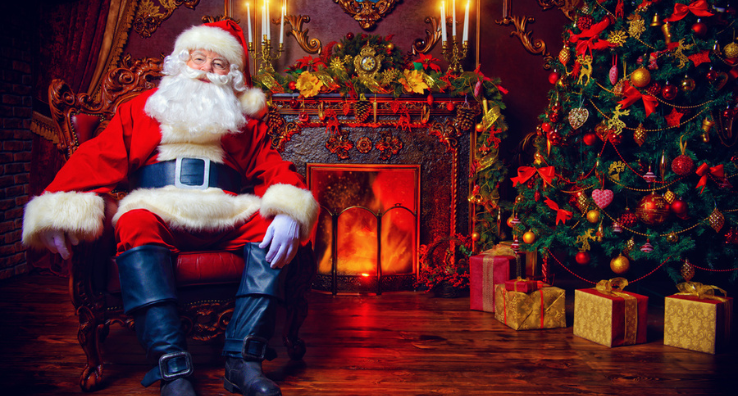
Santa’s workshop maintains a 24-hour production line that has built toys for millions of children worldwide for hundreds of years. Surely there have been one or two accidents along the way. How could there not be?
Just think about all those slippery floors from snow-covered boots. Elves work impossibly long hours with ridiculously repetitive tasks. Large equipment runs nonstop. And don’t forget those perilous moments when Santa has to save Christmas with a last-minute production rush.
It’s magical. But it’s also a recipe for disaster. Ho Ho, No!
Clearly, Santa could benefit from a safety regulatory body. But which one? Is the workshop considered a U.S. entity operating on foreign soil? If so, OSHA might apply. Or maybe he’s an international rogue operation that flies by the seat of his large red pants with no governing bodies.
Even if Santa is immune to all safety requirements, here are five things he can do to ensure his elf workforce consistently and safely achieve their production goals. They might also apply to your workshop.
- Throw in More Hot Cocoa and Safety Training Breaks
Research shows that companies providing at least 20 hours of annual safety training are 68% more likely to have employees following safety protocols on the floor. Even then, 66% believe, despite their best efforts, they still have employees who don’t follow workplace safety protocols on the floor, according to our report, The State of Workplace Safety Training. Elves are used to that black-and-white, naughty-or-nice culture, so they might be more inclined to follow safety training than ignore it. - Meet New Designs with Modern and Relevant Training
New toy designs arrive every year. Santa can’t count on his elves to learn the latest and greatest and keep production rolling at the same time. It’s too much. However, he can help them get up to speed faster with modern training relevant to the task at hand. Companies using site-specific photos or videos in training courses are two times more likely to have employees “very engaged” in their safety training. And companies using a learning management system (LMS) can provide 30% more training refreshers and reinforcement. We know from our research that when you use interactive audience response training technology, you are 58% more likely to verify if a specific employee – or elf – understood their training. - Keep Those Production Floors Safe and Dry
Slips, trips, and falls in the workplace are responsible for nearly 16 million injuries each year. Outside the North Pole, they are the second leading cause of fatalities on the job and the third leading cause of employee disability. Last year, slips, trips, and falls played a major role in more than 84% of all non-fatal injuries involving days away from work. Teach those elves how to use fall prevention equipment, be aware of their surroundings, and keep the reindeer games outside. Elves are vertically challenged, so double down on ladder safety training. - Create a Hazards List and Check it Twice!
Santa’s workshop is a complex and busy environment. The naughty list of hazards must be a mile long. Santa’s elves should be encouraged to call out hazards when they see them without getting into trouble. Santa should establish procedures that continually identify workplace hazards and evaluate risks. This means examining all processes and tasks, from the routine to the extraordinary, to identify related safety and health hazards. Periodic inspections and reassessments should follow his initial assessment to identify new and changing risks. Santa really needs to get over his ban on outside visitors and invite an expert to conduct a workplace safety compliance assessment. - Retain and Promote the Elf-force
Even in the elfin world, there are some other employment opportunities. It could be with that Keebler Cookie outfit or the not-so-friendly South Pole elves. Keeping the workshop elves happy and engaged with training programs that develop and promote from within is essential. One way of improving worker retention is to implement cross-training programs. Cross-training provides an opportunity for growth – like advancing from a jack-in-the-box tester to a master tinkerer in less than 490 years. Cross-training also helps Santa’s elves understand the importance of their role within the overall toy production line.
Will a massive toy recall or significant OSHA fine ever be tied back to Santa? Probably not that we’ll know about. Santa does have a lot of pull. But for every other manufacturer, safety and employee engagement is something to think about all year.