New Year, New Energy: Kickstart 2025 with Purpose and Precision
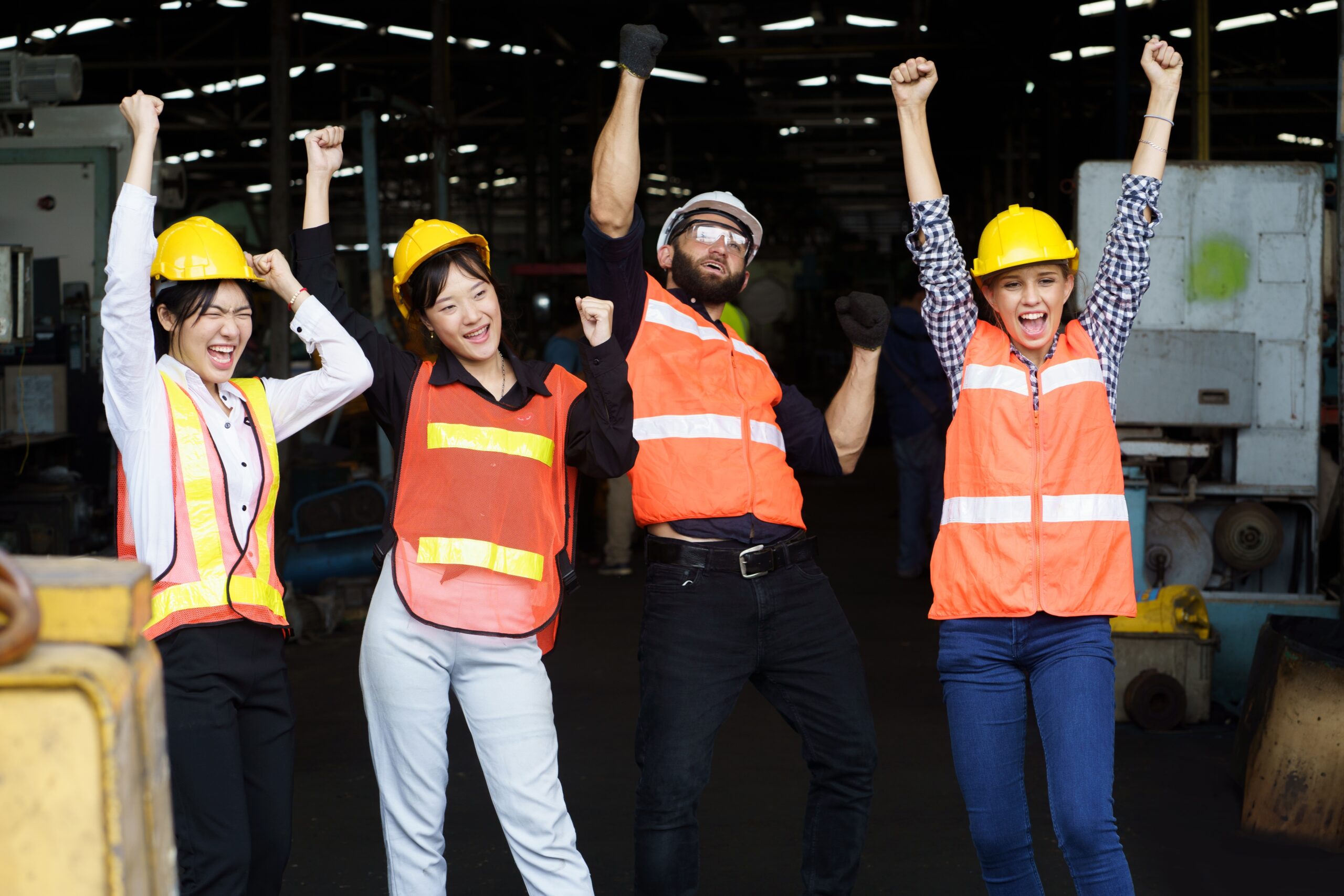
As the calendar turns to a new year, manufacturing facilities face an unparalleled opportunity to reflect, reset, and recharge their workforce. While automation technologies continue to shape the industry (as they have since at least the 1800s), the human element remains irreplaceable. A strong, skilled, and engaged workforce ensures not just stability but also resilience in the face of shifting demands and challenges.
Here’s how to start the year with energy, clarity, and a commitment to continuous improvement.
1. Embrace Human-Centered Automation
Automation will continue to evolve, but people remain at the heart of every facility’s success. While machines increase speed, they can’t replace the critical thinking, creativity, and adaptability of human workers. Investing in your workforce — through upskilling, cross-training, and continuous development — ensures that your company stays agile and ready to meet new challenges.
Pro Tip: Implement training programs that keep employees ahead of automation changes, such as the Alchemy Training System. The Alchemy Training System combines a range of learning approaches to foster engagement. And customizable skills development programs encourage a culture of continuous learning to reduce fear of displacement and facilitate growth.
2. Refresh Onboarding to Retain Top Talent
A structured onboarding process not only improves employee retention but also accelerates productivity. The start of the year is an ideal time to review and refresh onboarding procedures. Use audit findings or employee surveys to pinpoint areas of improvement and introduce tailored training topics that address gaps.
Pro Tip: Customize onboarding content with new training modules specific to your company’s needs. Early investment in new hires establishes a strong foundation for engagement and performance throughout the year.
3. Conduct Internal Audits: “The Road to RIO”
Internal audits — focused on records, interviews, and observations (RIO) — offer an essential way to evaluate and improve processes. January’s “fresh start” mentality is a perfect time to conduct internal audits that assess last year’s performance and inform your strategy for the year ahead.
Pro Tip: Most agencies that perform audits provide guidance documents outlying their process. Use these guidance documents to conduct audits like a third-party auditor and utilize software like Alchemy Coach to easily build and conduct the internal audits. This approach identifies potential non-conformities before official inspections, allowing for corrective actions that strengthen your quality efforts…and compliance.
4. Energize Employee Communication
Revamping how you communicate with your team can have an immediate impact on engagement and safety. Whether it’s launching a safety newsletter or revitalizing your quality committee, clear, transparent communication creates trust and accountability.
Pro Tip: Create opportunities for frontline employees to bring concerns to leadership or flag potential risk areas. Celebrate wins to maintain morale and motivation.
5. Prioritize Employee Mental Health and Well-being
Employee well-being — both mental and physical — has a direct impact on motivation, safety, and overall job satisfaction. Addressing mental health in the workplace shows employees you care about them as more than a metric and strengthens engagement. If you’re struggling to get approval to carve out time for this training, point out to the bean counters that healthier employees generally perform better and do more.
Pro Tip: Training leaders can’t be an expert in everything. For life skills and mental health training, leverage third party content that includes these topics in their course catalog.
6. Stay Current with New Regulations
The new year is a good time for manufacturers to look at the calendar for upcoming regulatory changes and customer-driven requests for new compliance measures. Food manufacturers should look at GFSI roadmaps in addition to FDA and USDA regulatory agencies. Proactively preparing for these changes reduces disruption and ensures ongoing compliance.
Pro Tip: Keep open communication with frontline workers who may not be in-the-know about regulatory changes. If a change is implemented, explain why. Also, ensure any third-party training content utilized has a process in place to update their content when necessary. For example, Intertek Alchemy’s course development process includes a dedicated team to update content as needed and deploy the updates to every facility using that content.
7. Foster a Culture of Continuous Improvement
Organizations committed to continuous improvement see better operational efficiency and higher employee engagement. A 2025 Culture Improvement Action Plan ensures that product quality and operational goals are consistently met.
Key Elements of the Plan:
Leadership Commitment: Demonstrate executive support for safety culture as a key organizational objective. Food manufacturers should have a separate objective in place for food safety.
Employee Engagement: Empower employees to recognize risks, escalate issues, and participate in recognition programs.
Continuous Improvement: Use Gemba walks, employee surveys, and supervisor coaching to sustain and improve safety behaviors.
Pro Tip: Conduct quarterly reviews to measure the effectiveness of your strategy, and adjust the plan as needed to ensure continuous improvement.
8. Lean Into Lean Manufacturing
With an increased emphasis on cost reduction and efficiency, Lean manufacturing will continue to be a major focus in 2025. This approach emphasizes waste reduction while increasing value to the customer.
Pro Tip: Most organizations only train leaders on the principles of lean manufacturing. Get your frontline workers involved with a lean training program that includes them, with more advanced training for leaders. When employees understand how their actions contribute to efficiency, they’re more likely to support lean initiatives.
9. Sharpen Business Skills for the Modern Workplace
As digital communication grows, email etiquette, electronic correspondence, and virtual meetings have become critical representations of your brand. Employees need training on effective digital communication and cybersecurity to protect the company’s reputation and assets. It also gives production workers opportunity to learn basic skills needed to advance their careers within your company.
Pro Tip: Provide courses on Microsoft Office, cybersecurity awareness, and digital communication best practices. Ensure employees can recognize cyber threats and know who to report them to.
10. Get Ready for Change Management
Change is inevitable in 2025, whether it’s new regulations, industry updates, leadership transitions, or customer demands. Preparing for change before it happens allows for smoother transitions and sustained momentum.
Best Practices for Change Management:
Review communication tools to improve cadence and clarity.
Train leaders on key change management skills.
Examine past challenges with change and seek new solutions.
Ensure strategic thinking and big-picture alignment.
Train leaders on active listening and conflict resolution.
Pro Tip: Conduct training sessions on change management skills for leaders. Encourage a proactive approach to adapting to change by identifying potential roadblocks and developing solutions. Help managers roll out changes to workers by providing “soft skills” leadership training. Equip them to navigate change with confidence and empathy.
Start Strong in 2025
The new year is more than a date on the calendar — it’s an opportunity to strengthen your workforce, refine your processes, and achieve sustainable growth. By focusing on human potential, continuous improvement, and operational excellence, your facility can meet the challenges of 2025 head-on.
If you’d like to start 2025 off strong with Intertek Alchemy, please contact us to learn more.