Supply Chain Verification: It Matters, So Mitigate Your Risk
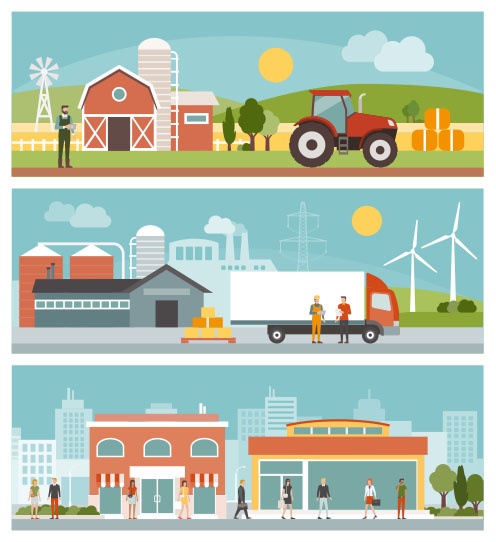
Supply chain verification failures are just as serious as main-line processing failures. They can lead to foodborne illness, death, and expensive litigation, which can seriously impede a company’s ability to do business. Companies should proactively and diligently manage their supply chain to decrease their risk of product recalls—and their accompanying, potentially catastrophic financial and brand damages.
To proactively address issues of product contamination and foodborne illness, food companies use various types of quality assurance and supply chain verification tools, including:
- Hazard Analysis & Critical Control (HACCP) plans
- Food safety plans with preventive controls for process, allergen, supply chain, and sanitation
- Supplier approval, risk assessment, and disqualification programs
- Risk assessments on suppliers, raw materials, packaging, and processes
- Recall, crisis management, and business continuity plans
- Second- and third-party food safety and quality audits
- Historical documentation
- Working relationship between quality, procurement, and R&D teams
- Ingredient, work-in-progress (WIP), and finished good specifications
- Sampling and testing programs
- Ingredient and finished goods label reviews
- Letters of guarantee
- Certificates of analysis and conformance
- Recordkeeping requirements
- Food defense protocols
- Quality assurance/quality control procedures
- Farm-to-fork traceability requirements
Companies that adhere to these standards basically have a supply chain verification system already in place. Food processing companies subject to FSMA requirements that rely on suppliers to control an identified food safety hazard are required to have a written supply chain program and methods of verification pre-identified for those suppliers. The objectives of supply chain verification include the following:
- Every product must be traceable back to its source
- Ingredients, WIP, and finished products are safe as intended if there is no accidental or intentional adulteration
- Food contact packaging is designed for its intended use
- Ingredient or product handling, transportation, and processing maintain product quality and safety
Acceptable methods of supply chain verification include one or more of the following:
- Annual third-party audits
- Sampling and testing by the supplier or receiving facility
- Review of food-safety-related records
- “Approved supplier” verification, receiving inspections, or others as appropriate
Second- and third-party food safety inspections or audits are valuable, but they have limitations. The effectiveness of inspections and audits could be enhanced by the end user requiring that its supply base undergo unannounced audits by recognized audit firms, using recognized food safety standards such as those established by the Global Food Safety Initiative (GFSI) or other recognized standards. As an alternative, end users could perform onsite second-party reviews of their suppliers.
These types of assessments can reveal an issue before a problem arises. If the end user relies on reviewing a third-party audit, what happens if the supplier doesn’t provide the complete audit and recommended corrective actions? Does that raise a red flag? Is the end user verifying the accuracy of the audit results or just the audit completion? If the facility in question does not follow the same stringent standards as the end user, the audit might not find an issue until the product reaches the marketplace, resulting in a potential recall.
One of the most challenging aspects of supply chain management is maintaining control of all the documentation required from each supplier and updating the information regularly. Manufacturers must have an effective way to communicate with each supplier to gather and review required information, including third-party audits, product specifications, letters of guarantee, supplier questionnaires, technical compliance documents, and numerous other forms. Forward-thinking companies use electronic food safety and quality system software with supplier compliance solution modules to simplify the process. It is highly recommended to use these systems to manage the critical food safety and quality system to properly control the massive amount of required documents and records.
Supply chain verification is not a new idea, but today it’s more critical than ever before. As the food safety system continues to expand globally and the supply chain is optimized and made smaller, reliable verification of an ingredient’s origins becomes one of the most important and effective ways of ensuring the safety and quality of subsequently manufactured products.
If you are at all unsure or worried about the competency of your suppliers, you should take the step of reassessing and strengthening your supply chain program. You must start with safe, high-quality raw materials to produce safe, high-quality finished products. As an industry, we have seen far too many recalls resulting from a single raw material source causing a weak link in the food supply chain. It’s time we make certain that robust food safety programs include effective supply chain verification methods to protect our businesses, our brands, and consumers.
{{cta(‘b1751a81-ae8b-4abd-be88-6351a49cd25c’)}}