Time is Running Out: How to Capture the Institutional Knowledge of an Aging Manufacturing Workforce
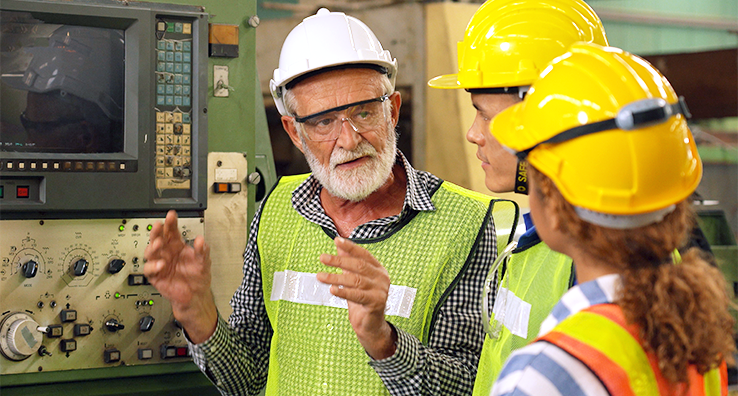
Currently, 27% of manufacturing workers are over the age of 66, which means many of your frontline staff and supervisors will be retiring within the next few years.
When an employee retires after decades of service, an enormous amount of practical and informative information leaves with them forever. Right now, there is an ever-widening gap in the manufacturing industry between jobs that need to be filled and the number of skilled workers capable of filling them. In fact, a recent study by Deloitte and The Manufacturing Institute found that nearly 2.4 million open positions will remain unfilled because of the talent shortage in U.S. manufacturing over the next decade.
While there are several reasons for the skills gap shortage, one major driving force is the retirement of baby boomers. This is why now it’s more important than ever to capture the institutional knowledge of your aging workforce before they retire, or it will disappear with them.
Identify Subject-Matter Experts, and Capture Their Expertise
Experienced workers possess intrinsic knowledge of best practices and specific nuances of their facility, many of which aren’t documented in any SOP. So, it’s critical to identify the veteran employees operating the different types of equipment in your facility and collect their institutional knowledge through interviews, videos, written documentation, or other types of media. By collecting the knowledge of older workers and subject matter experts, manufacturers can:
- Reduce time and effort spent onboarding new workers;
- Avoid mistakes caused by lack of information;
- Remember previous successes, so they can replicate them.
Thankfully, organizations can lean on new technology to help achieve this mission. Mobile solutions, like Alchemy Playbook, provide the power to record their best workers performing various tasks throughout the facility and quickly turn it into an interactive training course with instructions and quizzes.
These job-specific courses can then be given to less experienced workers right on the production floor. Delivering this training exactly where the work will be performed helps the learner understand more clearly and apply more precisely. This consistently accurate on-the-job training helps prevent bad practices from spreading and makes the onboarding process far more seamless.
Put Processes in Place to Share Institutional Knowledge
The millennial generation and baby boomer generation are very different in the way that they prefer to share information back and forth. While the millennial generation is adept at sharing information on social media types of formats in the workplace, baby boomers typically prefer email as their primary communication channel. It’s imperative to find a system or method to establish a social and collaborative way for both generations to have a free flow of information back and forth, so that they can be collaborative. By using technology, manufacturers can create a process to capture and create that tribal knowledge and make it easily accessible to people whenever they need it.
Other critical tips:
- Encourage your older workers to take on mentorship roles with employees who are going to be taking over their tasks when they retire.
- Create teams that are multi-generational to provide continuous skill and knowledge transfer each and every day.
For more information on how Alchemy Playbook helps industrial organizations capture the institutional knowledge of the aging workforce, check out AlchemyPlaybook.com.