Training is Key for Building Trust in Lean Manufacturing
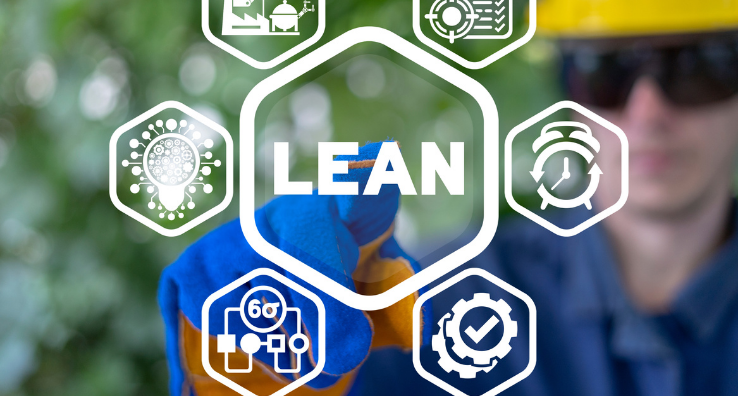
Lean manufacturing is synonymous with efficiency, which often leads people to believe Lean is all about reduction in the workforce or inventory. But efficiency is an outcome, not a strategy. Lean itself is a growth strategy. And like any strategy, it requires investment, not reduction, of time and resources to succeed.
I recently had the opportunity to host a webinar with Petra Sterwerf, Director of Operations at Skyline Chili, about implementing and sustaining Lean manufacturing systems. Petra is a long-time Alchemy client, a pioneer and one of the foremost experts on Lean principles in the U.S., and someone I truly admire in the industry.
Petra laid out some compelling recommendations on the benefits of Lean process improvement, implementation steps, pitfalls to overcome, communication techniques, and of course training best practices. Below are three takeaways from the webinar, which can be seen in its entirety here: The Art of Lean: Recognizing Waste & What to Do About It.
1. Lean is All About Inclusion
Engaging your workforce is always important for rolling out new strategies, but it’s absolutely critical for a successful Lean implementation. Taking steps to ensure workers fully understand how the Lean process can provide long-term prosperity and engenders mutual respect. When workers are enthusiastic adopters, they take pride in the efficiency, safety, and customer service improvements that bring a competitive advantage.
But before you take an initial step toward Lean, it’s essential to ensure employees not only understand the spirit of Lean but fully embrace the process. To establish this buy-in, mapping is essential in the beginning so everyone in the organization can visualize where the waste is and understand how their decisions impact other processes.
2. Adopt the Spirit of Experimentation
Even though we hear all the time that it’s ok to fail and learn from mistakes, it’s still hard for people to accept. Failure is absolutely necessary for continuous improvement, and it’s one of the most important factors in the overall success of the Lean process. Implementing a Lean system requires managers and workers to try new things, some of which will work and some that won’t. Looking at every defect or idea that didn’t work is a treasure because you can learn valuable lessons from each one. A good rule of thumb for all Lean improvements is plan, do, check, adjust.
As a manager, how you react to failures sets the tone. So, stay positive and encourage a culture of trying new things without fear of failure. That being said, continuous improvement managers should always ask questions before implementing a change to help their teams process what could happen and mitigate the risks.
3. Training Builds Trust
Companies that show they value employees enough to provide them ongoing training build loyalty and trust. To ensure Lean training fits into the overall learning strategy, it’s a good policy to include HR from the beginning. One great way to teach Lean concepts and engage workers is through one-day simulations using LEGOs or other fun modeling tools.
Line worker “training buddies” are critical for new workers to get up-to-speed on Lean efficiencies. But be careful about overloading employees who also have to monitor complex processes while simultaneously teaching the steps involved. Adding training coordinators to complement line workers relieves them from shouldering all of the burden. These coordinators can also act as junior change agents for Lean concepts, performing 5S audits and bringing fresh ideas to the table.
These insights from Petra are the tip of the iceberg. I encourage you to watch the entire webinar to dive deeper into the Lean experience.
In an effort to bring structure to the Lean training strategy, we recently rolled out the Alchemy Lean Manufacturing Training Module in our Premium Library, which consists of 10 e-learning courses that help managers and supervisors identify and eliminate inefficiencies and production waste in their organizations. Each course ends with knowledge check questions and a call to action to encourage the learner to practice what they learn on the shop floor. I’m proud to say that Petra added her expertise, which greatly informed the course content.
Feel free to reach out to us if you’d like to learn more about how the Alchemy Lean Manufacturing Training Module can jumpstart your Lean journey.