Turn Training into Learning with Multi-Touch Programs
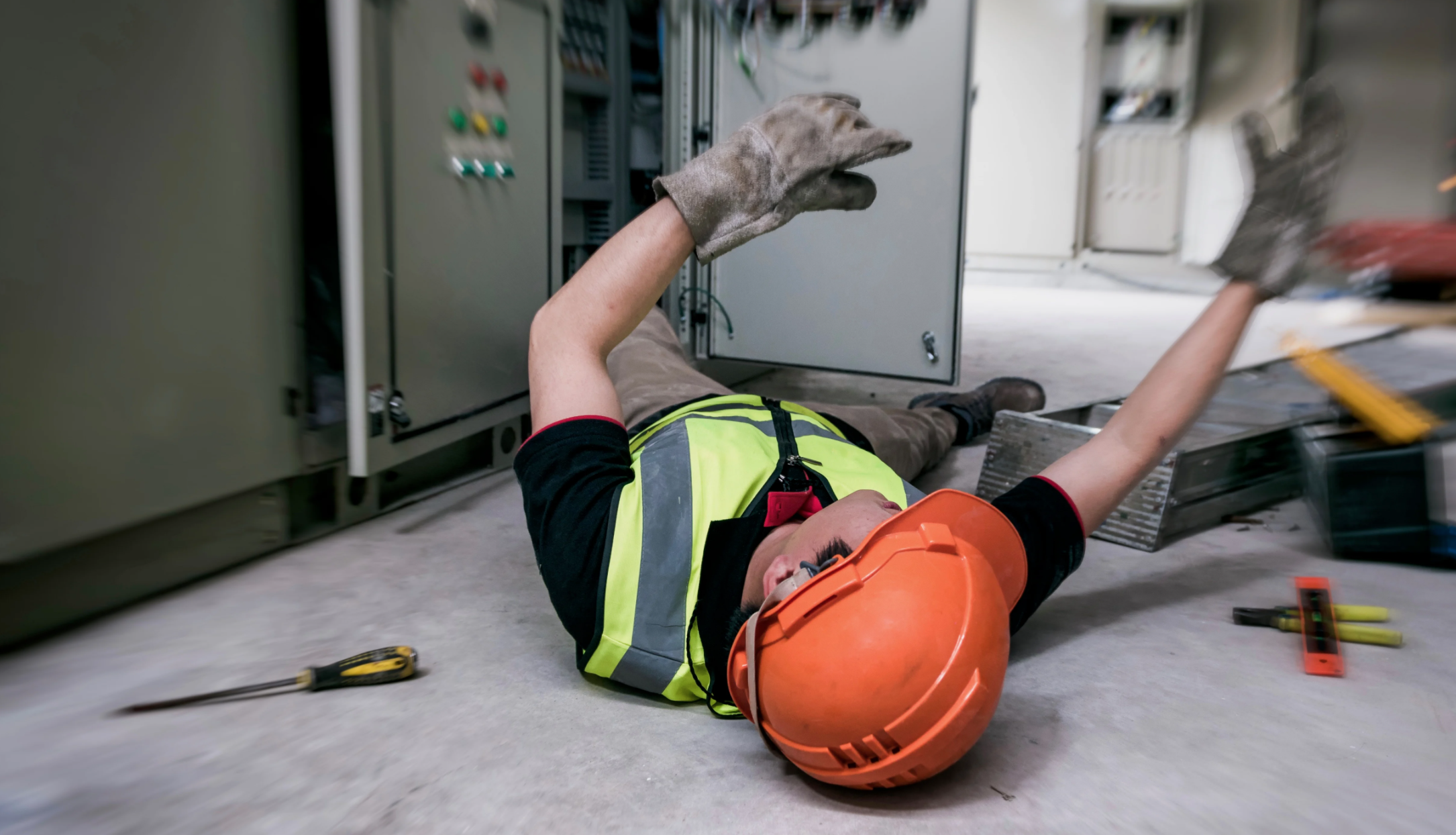
Workplace safety incidents cost American companies billions each year. Are you confident your employees have the knowledge and confidence required to prevent workplace injuries 100% of the time? If not, what are some effective ways to bolster their strength?
Studies show that while knowledge is important, confidence is also necessary to taking correct action. While knowledge depends on training, confidence depends on repetition and reinforcement. The more your workers know and understand workplace safety, the more likely they are to follow it.
Engagement Leads to Retention
One key to building confidence is engaging employees. Today’s workers span generations, education levels, and languages. Add to that challenge the growing number of distractions in today’s technology-driven culture — and finding fresh methods of engaging frontline workers is more critical than ever. Companies are only as strong as their people. Data shows the more frontline workers feel valued and engaged, the more likely they are to perform well and stay at their jobs.
Meaningful engagement begins with onboarding — but at many companies, this is also where it ends. A successful work safety training program depends on keeping safety training top of mind. This means repeating and reinforcing knowledge on a day-to-day basis, until messaging becomes so ingrained it manifests as “smart action at work.” This type of mastery can be accomplished with the right training and reinforcement tools. The key is delivering important messaging in short, multi-media formats — like video signage, posters, mobile apps, and huddle guides — for a deeper impact. Engaging employees not only raises worker retention rates, engagement strengthens comprehension.
How to Find Time to Train
Besides reaching a diverse workforce, one major obstacle to many safety programs is finding the time to train beyond onboarding, and perhaps more importantly, reinforcing training and validating comprehension. With tight production schedules and lean staff, taking time off the floor is not always an option.
Some leading companies have found success using mobile observation tools that allow them to train on the floor. Pre-written observation guides enable even the most novice or introverted supervisors to perform knowledge checks and corrective actions in the moment. Mobile tools like tablets with prescribed supervisor scripts can be used on the production floor without having to pull workers off the line. One-on-one interaction between team leads and workers is proven to facilitate comprehension, as well as foster engagement.
Reinforce, Refresh, and Repeat
Other reinforcement tools work well to solidify knowledge and they complement onboarding and training courses. Eye-catching posters and digital video placed in high-traffic areas make an impact by putting safety topics front and center. Rotating topics on a regular basis covers more ground, and keeps concepts fresh for a lasting impression. When workers receive safety messaging around the clock, they’re more likely to remember what they have learned, and even internalize safe behavior so it becomes automatic.
Refresher trainings are also helpful. In fact, studies show shorter sessions that encourage “active learning” are more effective than longer formats like lectures, manuals, or long video. Short learning “bursts” can take as little as three minutes and encourage retention. A learning management system (LMS) makes it easy to deliver role-specific learning plans with automatic refreshers on a set schedule. A good LMS also pushes automatic updates to leaders, so training management stays informed. If someone misses a refresher, training management is notified. A complete training system that incorporates a suite of tools is the best way to improve operations and reduce injuries.
What are some successful ways you’ve kept training continuous at your company? Share your comments below!